A many layered affair
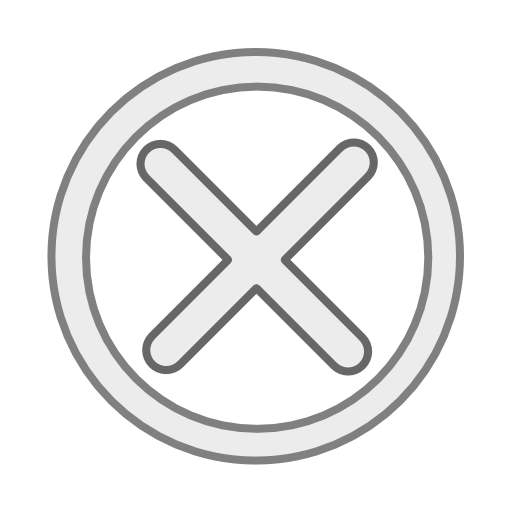
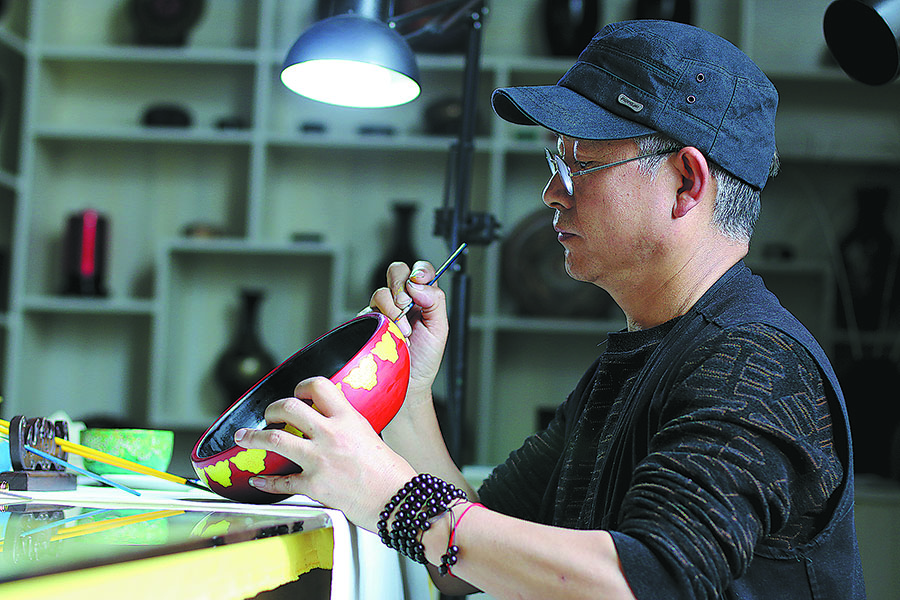
Records show that people of Yi ethnic group have long used raw lacquer to coat things like saddles and quivers. Subsequently, cowhide was used to create the embryos — the base of each piece — onto which layers of lacquer are applied, in stark difference to other popular lacquerware traditions that use wood, bamboo or cloth as their base.
Through a series of manual processes, the leather merges with the lacquer and is used to make wine vessels, tea sets and other daily items. The craft was systematically refined during the Ming Dynasty.
"It takes at least half a year to produce a lacquerware piece," Gao says, adding that this involves 50 steps spread across five main processes, including lacquer-making, embryo-making and decoration.
"First of all, premium lacquer itself doesn't come easily," Gao says.
Local craftsmen concur that it is only possible to get half a kilogram or raw lacquer after tapping trees thousands of times.
To make the cut, the lacquer should be as clear as oil when exuded and take on a striped texture like tiger skin when churned, and it should pour slowly in an unbroken flow. More specifically, it should retain 70 percent of its original weight after being heated to remove water. The heavier the weight, the better the hardness and glossiness of the final products.
After the lacquer is dried, trimmed cowhide is soaked in water for half a day to make it softer and easier to stretch before being nailed to a wood board, ready to be coated with a layer of mixture containing lacquer and a local type of yellow earth.
"There is no fixed ratio between the yellow earth and lacquer, and these proportions require years of practical experience to determine," Gao says.
The mixture is then applied and polished multiple times to harden the hide while ensuring its surface remains smooth and pore-free.
The nails and wood board are then removed and the rough edges of the hide are cut, before the piece is shaped.
Lacquer is reapplied and left to dry before being washed and polished. This step is repeated until the surface gleams.
It is then ready to be decorated, which ranges from drawing and sculpting to the use of eggshell and mother-of-pearl inlay.
"Every step requires precision, so you must hold your breath and be meticulous," Gao says.
Once the decoration is done and dry, more lacquer is layered on top and then polished with different grades of sandpaper to reveal patterns.
Finally, a thin layer of rapeseed oil is applied and powder is sprinkled onto the finished piece for further polishing until it shines brightly like a mirror.
"I have practiced the craft for more than three decades, and I'm still learning," Gao says.